See This Report on Sheroz Earthworks
Table of ContentsEverything about Sheroz EarthworksAbout Sheroz EarthworksAbout Sheroz EarthworksNot known Details About Sheroz Earthworks How Sheroz Earthworks can Save You Time, Stress, and Money.
When professionals like Rasch Building and construction carry out a quality control system for their dozers, it aids them make fewer errors when rating. This system continually keeps track of the blade, makes tiny adjustments to the position of the dozer blade during grading and reduces rework. If the dozer does not grade the ground precisely as intended, the driver can straighten the dozer blade to correct small mistakes and make exact modifications to get to the wanted quality.When considering the acquisition of a grade control system for a dozer, operators will certainly require training on exactly how to use the system. New operators and skilled professionals have to know with the components of the 3D quality control system, consisting of the hardware (as an example, the sensors and receivers) and the software program elements.
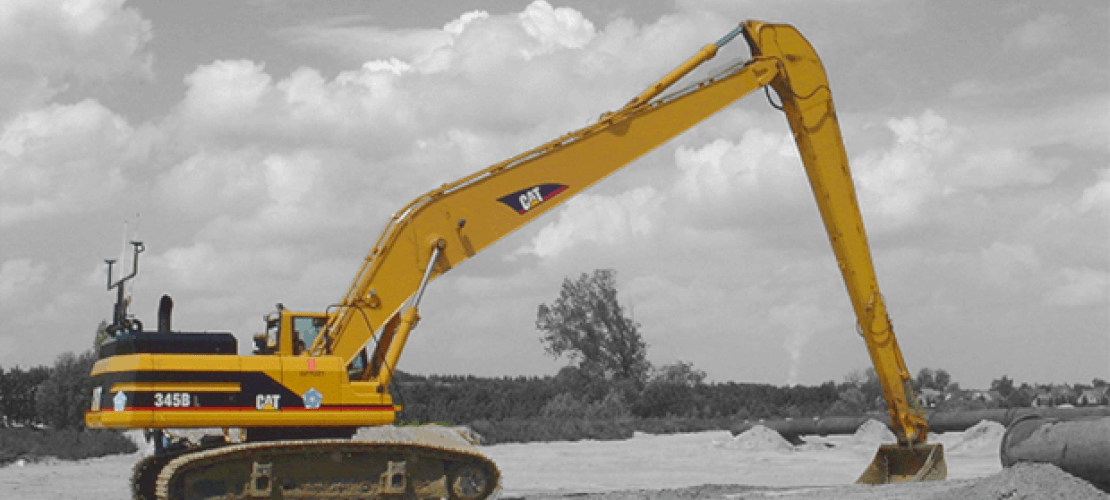
Sheroz Earthworks for Dummies
This consists of grade information, altitude data and other relevant metrics showed on the LCD screen inside the dozer's taxicab. Last, operator training need to consist of just how to efficiently control the dozer blade making use of the 3D quality control system. This assists them understand how the system changes the blade in response to grade variations.
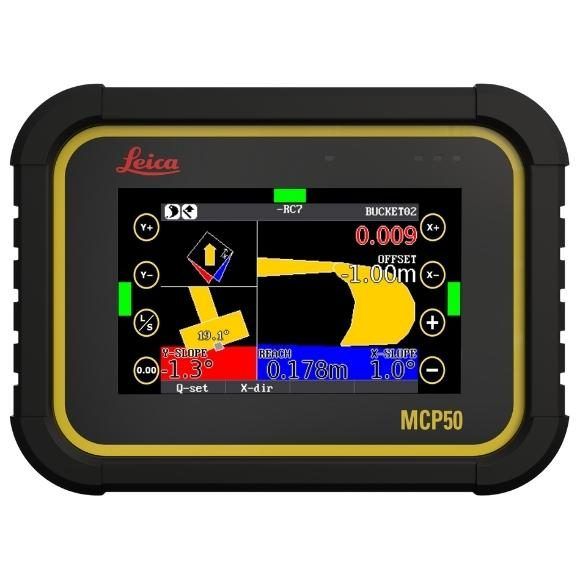
Product cost savings: If the grade is more accurate, a service provider may require less product for the jobsite. Operators might additionally minimize the need for rework and improve expense financial savings due to labor and materials - https://www.quora.com/profile/Floyd-Overbeck. To read more concerning how to boost jobsite effectiveness with grade control modern technology, explore the offerings from Trimble and comparable business
Guidance and precision control, the base elements of contemporary machine control for building and construction, have remained to advance considering that wide productization began in the mid-1990s. The value recommendation has actually come to be also sweeter because, with worth being understood beyond the return on investment (ROI) of the general specialists and the total task price tag for the clients - trimble gps.
Top Guidelines Of Sheroz Earthworks
The origins of maker control stretch back a century. The Historical Construction Tools Organization (HCEA) posits that the A.W. French & Co. "utility " of the 1920s, a crawler-mounted unit that made use of stringline control, may be the extremely initial example and this prior to electronic devices and computer. However, it was the development of real-time kinematics (RTK) for general practitioners in the mid-1990s that brought equipment control as we know it to the building site, and together to precision farming.
It moved to accuracy control, such as blade control, and later circulated to more courses of motorized devices, boosted with more sensing unit combination. The influence on building and construction and farming has actually been undeniable: performance gains, much less rework, a lot more efficient handling of materials, shorter timelines, website safety renovations, and a lot more - https://my-store-f82e47.creator-spring.com/. These benefits are as evident to clients and operators as they remained in the early days of fostering, gains from almost 3 years of advancement
Automation is not nearly speed; it is likewise about much better control of the load and stress and anxiety on the tools and relocating simply the right amount of products so as not to position a burden on it. (Photo: CHCNAV) These 2 activities, as each of our interviewed professionals testify, represent the lion's share of understood productivity gains.
The smart Trick of Sheroz Earthworks That Nobody is Discussing
"Apart from the skid guide systems, there are more excavators manufactured than all the other tools types integrated," stated Daniel Sass, item supervisor of equipment control at Hemisphere GNSS. "Excavators are the workhorse. And people use them in different ways, and they utilize various other tools to complement excavators rather in a different way.
Definitely, by quantity it is excavators and small excavators." Numbers help inform the story. "In the United States, at the very least in a three-year period from 2019 to 2022, concerning 253,000 excavators were sold, for which I have pretty reliable data, however only 61,000 dozers and only 7,000 scrapers," Sass claimed
If you go to Europe, where they make use of excavators for many other jobs, the symmetrical impact may be greater." Operators the original source can conveniently evaluate the ROI of going digital for individual tools such as excavators, yet component of the incentive might be that general specialists are needing subcontractors to be furnished and ready to fit into an extra full electronic site.
"A lot of larger websites. "Just how do you move the product? With operator assistance, Clark said, it is not unusual to see productivity gains of 30% to 40%, even with inexperienced drivers.
The 4-Minute Rule for Sheroz Earthworks
There are substantial gains to be made in driver help for less facility heavy equipment, such as compactors. "Frequently a contactor will certainly put a less knowledgeable driver in the compactor," Clark claimed. "In manual days, to get rid of the potential of under-compaction and missing spots, they 'd develop fairly a huge overlap, perhaps as much as 40% of overlap in between courses.